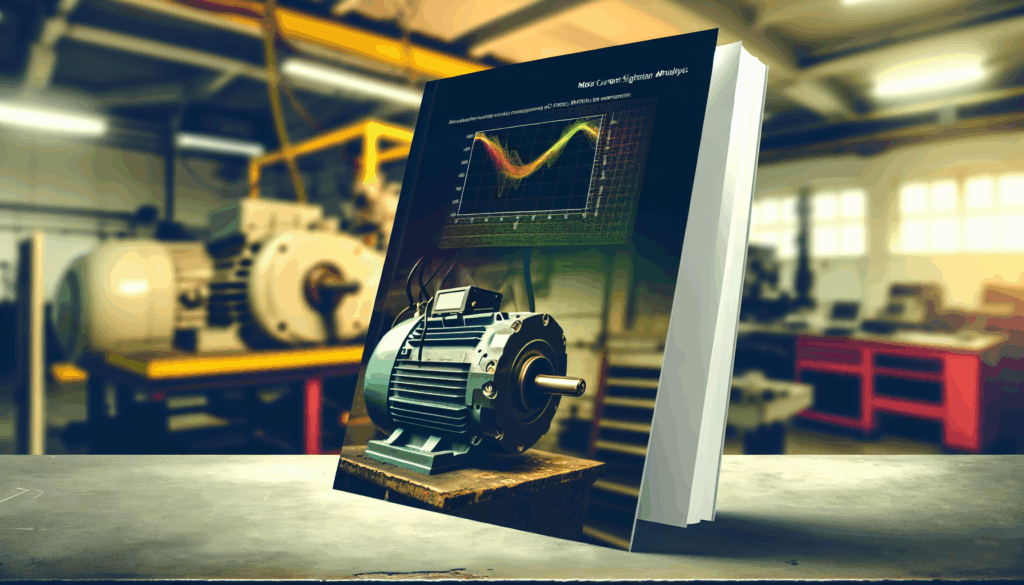
Foreseeing Motor Failures: The Power of Motor Current Signature Analysis
Motor failures can bring operations to a grinding halt, but with Motor Current Signature Analysis (MCSA), you can detect problems before they escalate. Discover the steps to incorporate MCSA into your motor maintenance routine and ensure maximum uptime in this insightful article.
Understanding Motor Current Signature Analysis
Understanding Motor Current Signature Analysis (MCSA) demands an appreciation for the basics of how electric motors operate and the common ways they can fail. At its core, MCSA is a powerful predictive maintenance tool that analyzes the current signal emanating from a motor while it’s in operation. Essentially, MCSA scrutinizes the tiny variances in the motor’s current that can signify underlying issues such as bearing failures, rotor bar defects, and air gap eccentricities, among others. By detecting these early signs of wear or malfunction, MCSA enables maintenance teams to address problems before they escalate into costly failures.
The process of MCSA involves the collection of current data through sensors attached to the motor. This data is then subjected to detailed spectral analysis to identify any abnormal patterns or signatures that deviate from the norm. The beauty of MCSA lies in its non-invasive nature and the minimal downtime it requires, as data collection can occur during regular operation.
One of the chief benefits of incorporating MCSA into a predictive maintenance strategy is its ability to transition maintenance efforts from being reactive to proactive. Instead of waiting for a motor to fail, maintenance teams can anticipate issues and undertake corrective measures in advance, thus significantly reducing unplanned downtime and associated costs.
Practical examples of MCSA in action span across various industries from manufacturing to energy. In one instance, a paper mill utilized MCSA to detect a hidden bearing flaw in a large press roll motor, preventing what would have been a catastrophic failure. Similarly, a utility company employed MCSA to identify and rectify a misalignment in a critical pump motor, averting a potential disruption in service. These examples underscore the versatility and effectiveness of MCSA in diverse operational contexts, offering invaluable lessons for organizations aiming to bolster their maintenance regimes. Adopting MCSA allows enterprises to not only enhance the reliability and efficiency of their motors but also significantly optimize their maintenance expenditures.
Conclusions
Motor Current Signature Analysis (MCSA) is a crucial tool in the predictive maintenance toolbox. By understanding and implementing MCSA, facilities can significantly improve uptime and reduce costly unplanned downtime. As we’ve seen, the practical steps to MCSA can transform maintenance strategies and contribute to overall operational excellence.