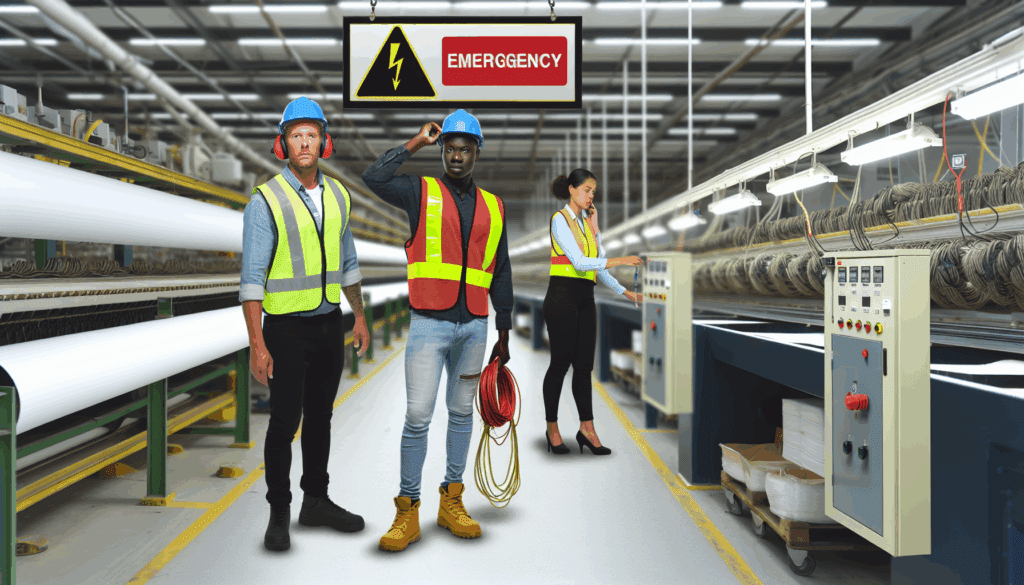
The Great Save: How Quick Actions Averted an Electrical Crisis at a Textile Factory
Picture a regular day turned into a potential catastrophe: a textile plant on the brink of an electrical meltdown. This is the story of how swift decision-making and emergency protocols saved a facility and its workers from disaster. A testament to the importance of preparedness, let’s uncover the actions taken in this harrowing ordeal that are essential in any industry.
The Perils of Electrical Disasters in Textile Manufacturing
In the high-stakes environment of textile manufacturing, electrical risks such as power surges, equipment failures, and static electricity loom large. The presence of flammable materials such as fabrics and dyes significantly escalates the potential for disasters. Specifically, power surges can overwhelm electrical systems, leading to fires that rapidly consume materials and jeopardize lives. Equipment failures, on another front, may cause sparks—igniting textiles and engulfing factories in flames. Furthermore, static electricity, often overlooked, poses a serious risk, capable of causing explosions in environments laden with flammable dust or fumes.
The challenge in managing these risks is multifaceted, necessitating vigilant maintenance and robust emergency response plans. Regular inspections and maintenance of electrical equipment are critical in identifying potential hazards before they lead to disaster. Similarly, emergency response plans that are specific to the scenarios unique to textile manufacturing—accounting for the rapid spread of fire through flammable materials—are indispensable.
Real-world incidents highlight the devastating consequences of negligence in this arena. For example, a factory fire in Bangladesh underscored the lethality of these hazards when inadequate safety measures allowed a minor electrical fault to result in catastrophic loss of life.
To mitigate these risks, the implementation of comprehensive safety measures is paramount. This includes training personnel in fire safety and disaster response, ensuring that all employees are equipped to act swiftly and efficiently in the event of an emergency. By fostering a culture of safety, emphasizing the importance of maintenance, and preparing meticulously for potential disasters, textile manufacturers can safeguard against electrical hazards, minimizing damage and ensuring the wellbeing of all personnel.
Conclusions
The story of the textile plant’s rescue from electrical doom is more than just thrilling; it’s educational. It emphasizes the importance of risk management and response preparation in industrial settings. Through this case, we learn that constant vigilance, regular maintenance, and proper training are non-negotiables to ensure the safety of both workers and facilities. It is a clear call to action for all sectors to strengthen their emergency protocols and become uptime champions.