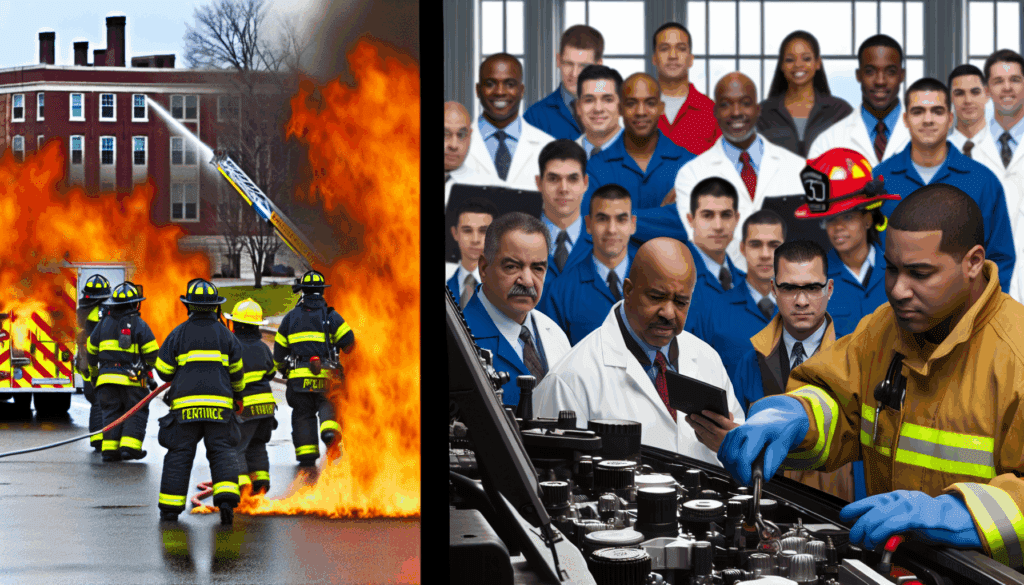
From Firefighting to Foreseeing: The Evolution of Maintenance Strategies
In a world of constant demand, maintenance strategies can make or break the success of your operations. This article delves into the transformative shift from reactive to proactive and predictive maintenance, offering actionable insights for optimizing uptime and efficiency.
Understanding Reactive, Proactive, and Predictive Maintenance
In the traditional reactive approach to maintenance, tasks are performed after a failure occurs, leading to unexpected downtime and often more extensive damage than if the issue had been addressed beforehand. This method, while straightforward, results in higher repair costs and operational inefficiencies as equipment is often used until it breaks down, disregarding the potential for preemptive intervention.
Proactive maintenance emerges as a significant advancement, focusing on preventing equipment failures before they occur. By identifying and addressing the root causes of equipment deterioration—such as wear and tear, environmental conditions, and operational stresses—this approach aims to enhance the reliability and longevity of assets. Routine inspections, lubrication, adjustments, and parts replacements are typical proactive measures that, though initially more resource-intensive than reactive maintenance, significantly reduce the long-term costs and occurrence of unplanned downtime.
Predictive maintenance takes this concept further by utilizing data collection, statistical process control, and advanced technologies such as machine learning to anticipate when maintenance should be performed. This strategy relies on condition-monitoring tools and techniques to accurately forecast potential failures and schedule maintenance activities in a highly efficient manner. Real-world applications, for instance in the aerospace industry, have demonstrated how predictive maintenance can dramatically extend the life of aircraft components, optimizing flight schedules and minimizing operational interruptions.
The shift toward proactive and predictive maintenance strategies marks a critical evolution in asset management, highlighting the importance of foresight in today’s industrial environment. By moving away from the reactive model and embracing these advanced approaches, organizations can significantly improve equipment reliability, reduce maintenance costs, and enhance overall operational efficiency, a necessity in the competitive, productivity-driven market landscape.
Conclusions
Embracing proactive and predictive maintenance is not a fad but a fundamental shift in asset management. By applying the advice and steps outlined in this article, organizations can elevate their operations, foster safety, and maximize the lifespan of their equipment.