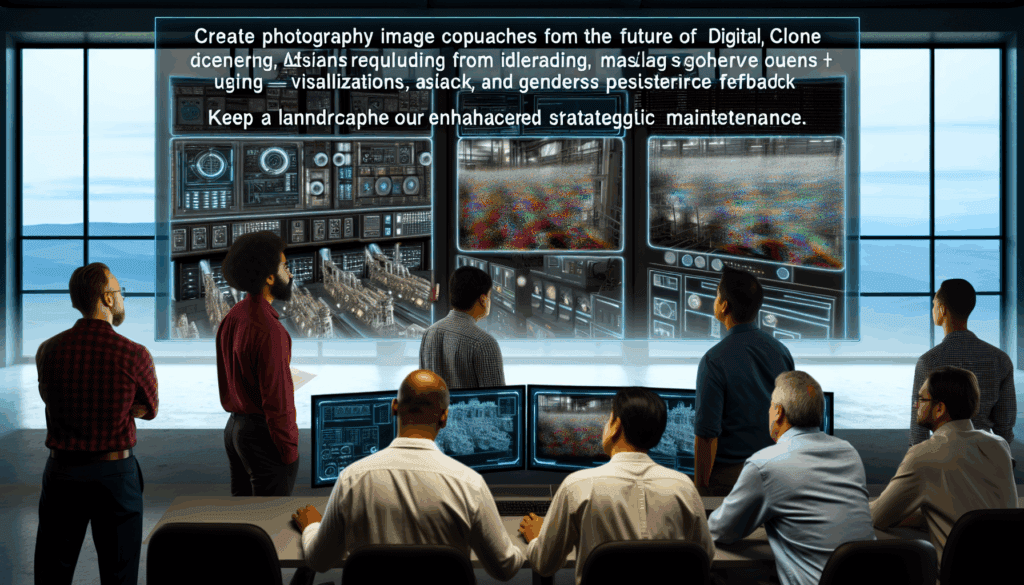
Harnessing Digital Twins for Enhanced Maintenance Strategies
Welcome to a journey through the advanced realm of maintenance technology. Here, we unveil how digital twin technology is revolutionizing the way we manage and maintain equipment. This article delivers critical insights into game-changing practices poised to transform daily operations with utmost precision and foresight.
The Role of Digital Twins in Predictive Maintenance
In the heart of modern maintenance lies the concept of the digital twin, a dynamic digital representation of a physical system that’s changing how we approach equipment upkeep. This chapter delves into the synergy between digital twins and predictive maintenance, explaining how this integration:
- Facilitates real-time monitoring and simulation of physical assets.
- Enhances decision-making processes with accurate predictive analytics.
- Minimizes unexpected equipment failures and downtime.
- Maximizes cost efficiency and resource optimization.
- Drives innovation and sustainability in maintenance practices.
- Leverages machine learning for advanced fault detection and time-to-failure prediction.
By enabling real-time monitoring, digital twins allow for the continuous assessment of equipment condition and performance, providing a basis for immediate adjustments and preventive actions. This dynamic simulation capability extends to predicting future states and behaviors under various scenarios, thus improving the precision of predictive analytics. Such advancements significantly lessen the likelihood of sudden machine breakdowns, which are costly in terms of both repair expenses and operational downtime.
Moreover, by applying machine learning algorithms to the vast datasets generated by digital twins, maintenance teams can identify subtle patterns that precede equipment failures, enabling even more nuanced and timely interventions. These capabilities not only augment operational efficiency but also foster an environment where resources are utilized more judiciously, aligning maintenance efforts with the principles of sustainability.
Through practical examples, it becomes evident that integrating digital twins into predictive maintenance strategies leads to substantial improvements in asset management and reliability. For instance, a manufacturing firm experiencing frequent unexpected downtimes might employ a digital twin to simulate different operating conditions and identify the root cause of machine failures. This proactive approach not only reduces interruptions but also extends the equipment’s lifespan and lowers maintenance costs.
Thus, the marriage of digital twins with predictive maintenance heralds a new era in industrial and facility management, where the emphasis shifts from reactive to proactive and predictive strategies. This not only champions innovation but also significantly enhances the sustainability and efficiency of maintenance operations.
Conclusions
In conclusion, the implementation of digital twins within predictive maintenance frameworks offers a transformative approach to ensuring the longevity and performance of equipment. By leveraging real-time data, machine learning, and advanced analytics, organizations can anticipate maintenance needs, prevent costly failures, and drive operational excellence. Embracing this innovative strategy is fundamental to staying ahead in an ever-evolving technological landscape.